News
Read the latest news, case studies & event reports from our Flow Community! Want to stay up to date? Sign-up for our newsletter & a few times per year we will e-mail you interesting articles, developments, up-coming event info!
Flow Technology Expands Process Understanding, Reaction Space & Process Control
27 June 2018
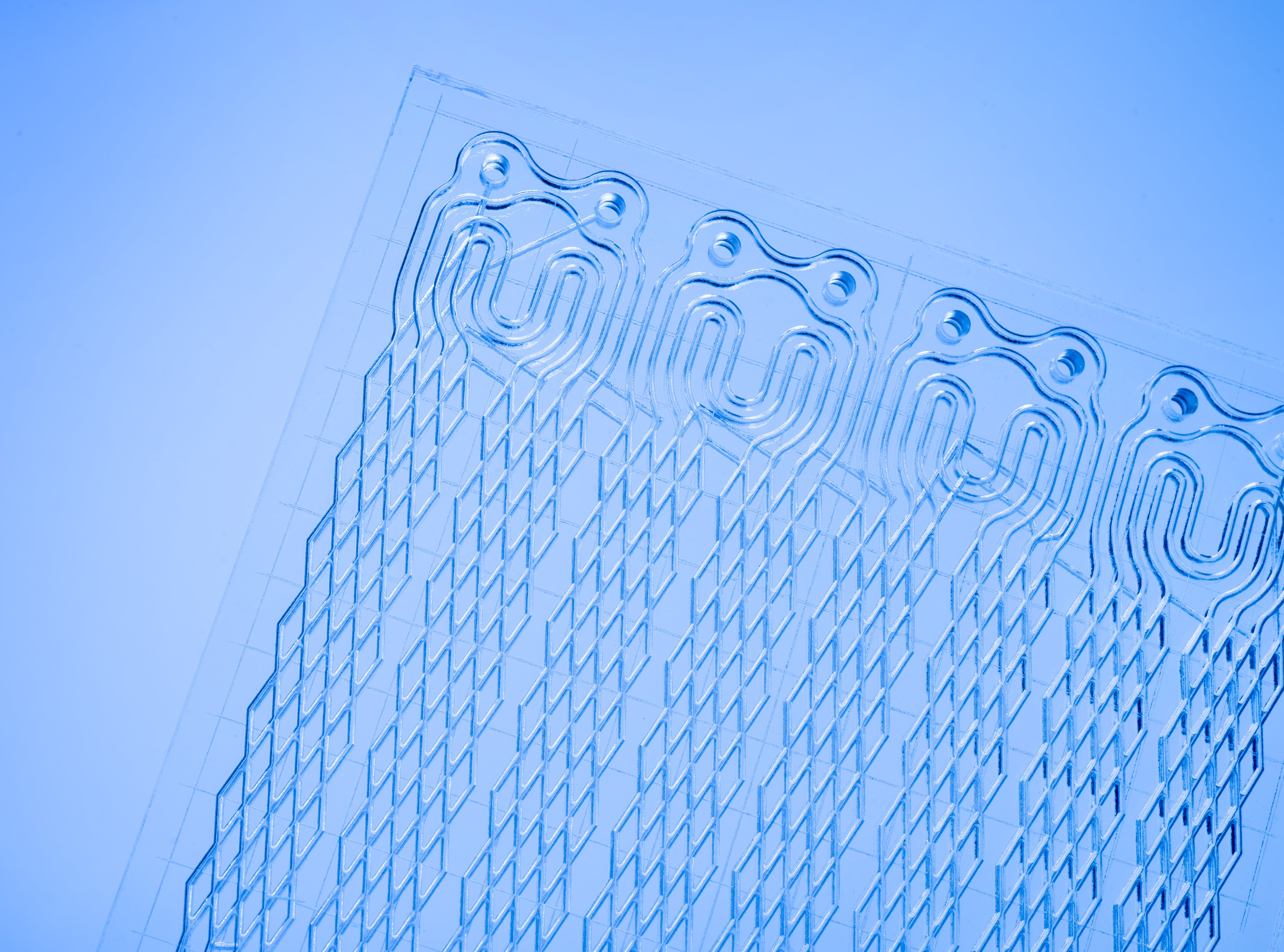
With mounting evidence at the lab & production scale that Continuous Flow Reactors can give access to not only new processing conditions & production scales, but also more stable & reproducible conditions for material manufacturing, examples of use include specialty chemicals, API’s & even continuously prepared solid doses (tablets).
So where to start?
Identifying your goals & targets for a new piece of research / process development is key!
Following on from this, experimentation should be designed to address the goals/targets – enabling you to determine where/how the technology can benefit you. This could be for example in the development of a more selective route to a target compound, a more intensive production method for ramping up capacity or to evaluate new opportunities using neglected techniques like photochemistry or electrochemistry.
Advantages:
Speed is a key advantage when researching! In flow, process conditions can be changed rapidly & the quantification of parameter influences performed on small quantities of material – giving increased insight & process understanding at an earlier stage of development.
Owing to the speed of parameter change, many research groups have explored the use of flow reactors for kinetic profiling, with several groups developing self-optimising approaches - such as super modified Simplex algorithms - with optimisation parameters including cost factors, not just the highest reaction yield.
As the effect of stoichiometry, reagent or solvents can be mapped using flow reactors, insight gained can also be applied to improve batch process(es) (assuming that the target conditions can be safely applied to the required batch-size). In up-coming editions of OPRD, Science & Nature you will see examples of such work from leading Global Pharmaceutical Companies.
Robust & reproducible process design is key for production!
Differences to Batch?
One striking difference to batch operation is that continuous processes are designed to operate in a state of control – where product composition is not changing with time (unless parameters change). Compared to a batch process where the product quality is often determined via offline evaluation after the reaction is completed, in a continuous process the product is generated continually – this presents opportunities to monitor in real time using process analytical technology (PAT) & employ Quality by Design.
The relatively short reaction times used can however present a challenge for conventional process monitoring approaches. When it comes to monitoring processes at a production scale to ensure operation is under a state of control there have been some impressive demonstrations of online-UPLC to assess critical quality attributes in API’s, together with the use of soft sensors such as conductivity measurements to confirm correct functionality of pumps & stoichiometric dosing. The technology is rapidly heading towards industry targets of real-time release – which signals a significant sea change from current practices of batch release.
Visit our Download Centre to learn more!