News
Read the latest news, case studies & event reports from our Flow Community! Want to stay up to date? Sign-up for our newsletter & a few times per year we will e-mail you interesting articles, developments, up-coming event info!
Successful Implementation of Continuous Flow Processes at CDMO’s
5 January 2021
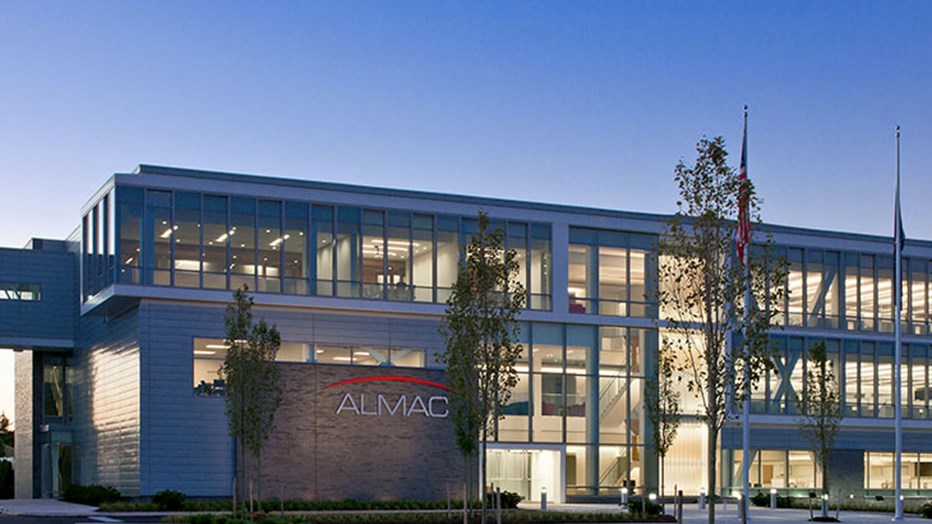
Whilst the major players in the CDMO space are seeing growth as business activities shift from ‘global to local’, this growth is realised not only by using expanded batch capacity, but also through the implementation of flexible continuous flow solutions. Prof. Tom Moody & colleagues at Almac Sciences suggest that for CDMO’s ‘The time is now to change & flow into the future!’.
Why Continuous Manufacturing?
The advantages of changing from batch to flow for primary processes are widely publicised to include increases in safety, process efficiency & product consistency; however, the drivers to change from ‘batch to flow’ vary & often depend on the sector, process type of interest & scale of operation. Examples include a speed to market, reduced cost of goods, efficient use of existing asset space & more recently supply chain security.
Platform Technology
Continuous manufacturing not only fills the gap, when batch capacity is reached, but it also enables the performance of chemistries that would not be conventionally considered at scale, due to the low hold-up volume, small footprint & increased process safety. The modularity & flexibility of continuous flow set-ups enables the development of small, agile production plants that can be used for the manufacture of multiple products – facile re-configurations allow for rapid product change-over. Using a four-stage project workflow has enabled Almac Sciences to develop robust, safe & scalable processes from multi-kg to tonne-scale.
Partner for Success!
With the uptake of continuous manufacturing rising in the fine, specialty & pharma sectors, we see an increase in projects that are actively up-scaling from proof of concept towards manufacturing. For successful CM implementation, our view is that a multidisciplinary approach is required to achieve the project goals of safe, efficient, cost effective manufacturing & should involve a mixed Team from the outset, obtaining the much needed ‘departmental buy-in‘ & expertise (Read More).
This concept was discussed, in part, by Almac’s Prof. Tom Moody in Chemicals Knowledge Hub, ‘Successful Implementation of Continuous Flow Processes’.
For further information contact:
Prof. Tom Moody | Dr. Charlotte Wiles |
Almac Sciences / Arran Chemical Company | Chemtrix BV |
VP Technology Development & Commercialisation | CEO |
tom.moody@almacgroup.com | c.wiles@chemtrix.com |
About Almac Sciences
The Company has a multidisciplinary Team consisting of both chemists & chemical engineers with extensive expertise in organic chemistry, suspension polymerisation, biocatalysis, enzyme immobilisation & process design & development for both GMP & non-GMP manufacture. Almac has significant Flow Chemistry expertise including high pressure, high energy, oxidations & photochemical transformations. www.almacgroup.com
About Chemtrix
Chemtrix BV offers a scalable flow reactor portfolio that affords researchers & industrialists the tools required to harness the advantages of primary continuous manufacturing. We combine expertise in the field of mechanical engineering, chemical engineering & chemistry to help our customers to benefit from the advantages that flow chemistry brings. Our expertise enables us to offer scalable & flexible flow chemistry solutions, focussing on delivering our Customers higher profits by accessing new chemical possibilities via a safe & reliable scale-up from lab to production-scale. Working closely with academia & industry, we work to change the way that chemical processes are developed & implemented. Our global user base spans research institutes & government laboratories to leaders in the fine chemical, specialty & pharmaceutical industries. www.chemtrix.com